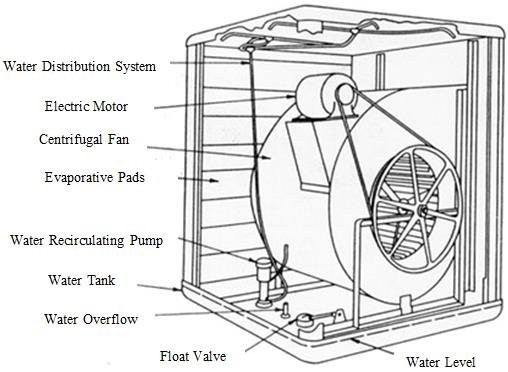
What Are Direct Evaporative Cooling Systems and How Do They Work?
July 24, 2025 7:47 pmIn the realm of climate control and HVAC technology, direct evaporative cooling systems represent one of the most energy-efficient and cost-effective methods for temperature reduction, especially in arid and semi-arid climates. These systems harness the natural cooling effect that occurs when water evaporates into the air, reducing air temperature without the need for energy-intensive refrigeration cycles.
Understanding the Principle: How Direct Evaporative Cooling Works
At the heart of direct evaporative cooling lies a fundamental physical process: the absorption of heat during water evaporation.
When unsaturated warm air passes over or through a wetted medium, it picks up water vapor. This phase change—from liquid to vapor—requires energy, which is drawn from the air’s heat content. As a result, the air’s dry-bulb temperature decreases, although its humidity increases. The cooled, moistened air is then delivered directly into the space to be conditioned.
This contrasts with mechanical refrigeration systems, which rely on the compression and expansion of refrigerants—a process that consumes far more energy.
The Psychrometric Basis of Evaporative Cooling
To fully appreciate direct evaporative cooling, one must understand basic psychrometrics, the study of moist air properties.
Key concepts include:
- Dry-bulb temperature (DBT): The regular air temperature.
- Wet-bulb temperature (WBT): The lowest temperature achievable through evaporation under current ambient conditions.
- Relative humidity (RH): The amount of water vapor present in air relative to the maximum it can hold at a given temperature.
Direct evaporative cooling lowers the DBT while pushing the RH upward. The process continues until equilibrium is approached with the WBT. Therefore, the cooling potential is the difference between the DBT and WBT—known as the wet-bulb depression.
In ideal conditions, a high-efficiency system can approach the wet-bulb temperature within 2–4°F, which translates to up to 98% cooling efficiency when using advanced cooling media.
Core Components of Direct Evaporative Cooling Systems
- Air Inlet and Distribution Assembly
Ambient air enters the system through strategically designed inlets, often protected by louvers and screens to prevent debris ingress. Proper distribution ensures uniform contact with the wetted media.
- Evaporative Media (Cooling Pads)
This is the core of the system—the location where the heat exchange occurs. Premier Industries, Inc. uses rigid-type high-efficiency media, which features engineered fluted cellulose or polymer materials with superior water absorption and structural integrity. Our media designs can reach up to 98% saturation efficiency, yielding excellent cooling performance.
- Water Circulation System
Water is pumped from a sump or reservoir and evenly distributed over the media. A carefully designed flow ensures the entire surface stays saturated without flooding, which could reduce airflow or lead to microbial growth.
- Air Movement System (Blowers or Fans)
Fans draw or push the air through the media. Centrifugal blowers or axial fans are selected based on static pressure and airflow requirements. Blower selection directly impacts energy use, pressure drop, and system performance.
- Casing/Housing
A high-quality evaporative cooler must resist corrosion, withstand environmental conditions, and maintain dimensional stability. At Premier Industries, Inc., we use lifetime stainless steel housings, which offer unmatched durability and hygiene, especially critical in industrial and food-processing environments.
- Drainage and Filtration
Proper drainage prevents water stagnation and scale formation. Optional filtration stages can be added to remove airborne particulates, supporting IAQ (Indoor Air Quality) standards and system longevity.
Key Performance Metrics for Evaporative Cooling Systems
When engineering or selecting a direct evaporative cooler, these performance indicators are paramount:
Saturation Efficiency
This measures how closely the outlet air temperature approaches the wet-bulb temperature. Under optimal conditions, high-efficiency systems like ours reach 90–98% saturation.
Cooling Capacity (BTU/hr)
The rate of heat removal depends on:
- Airflow rate (CFM)
- Inlet/outlet dry-bulb temperatures
- Air density and moisture content
It is commonly calculated using the formula:
Q = 1.08 × CFM × (T₁ – T₂)
Where T₁ is the inlet temperature and T₂ is the outlet temperature.
Energy Efficiency Ratio (EER)
Direct evaporative coolers often exhibit EERs above 20, with some exceeding 40—significantly outperforming traditional DX (direct expansion) systems.
Water Consumption
Water usage is a function of evaporative load and bleed rates for mineral control. Efficient recirculation and filtration systems can minimize waste.
Advantages of Direct Evaporative Cooling Systems
- Energy Efficiency
Unlike compressors and refrigerants, evaporative systems require only fan and pump energy. As a result, they use up to 75% less electricity than traditional air conditioning.
- Environmental Sustainability
Direct evaporative coolers use no harmful refrigerants (e.g., CFCs, HFCs), emit zero greenhouse gases, and have lower embodied energy over their lifespan.
- Low Operating Costs
Maintenance is limited to water quality management and occasional media replacement. The absence of high-pressure compressors or electronic control boards keeps long-term ownership costs low.
- Improved Air Quality
Since the systems continuously introduce fresh, filtered outdoor air, they enhance ventilation and reduce recirculated contaminants—an advantage in residential and industrial settings.
- Modular and Scalable
Systems can be configured for various airflow capacities, cooling demands, and filtration requirements. Premier Industries, Inc. offers full customization to match your operational footprint and performance targets.
Challenges and Considerations
While effective, direct evaporative cooling systems come with certain limitations:
- Climate Dependency: Ideal in hot, dry climates like the Southwestern U.S., but less effective in high-humidity regions.
- Humidity Rise: Because cooled air is moistened, it may not suit all indoor processes, especially those sensitive to elevated RH.
- Water Quality: Hard water can lead to scaling and media degradation. Filtration and bleed-off systems help manage this.
- Regular Maintenance: Pads, sumps, and pumps need inspection to prevent microbial growth or mineral buildup.
That said, many of these concerns can be mitigated through proper engineering, design, and maintenance planning.
Typical Applications of Direct Evaporative Cooling
Industrial Cooling
Warehouses, manufacturing plants, and foundries benefit from cost-effective heat abatement without mechanical refrigeration. These systems are ideal for spot cooling, process cooling, or general ventilation.
Agricultural and Livestock Facilities
Evaporative coolers maintain optimal temperatures in greenhouses and poultry houses, improving crop yields and animal welfare.
Commercial Buildings
Big-box retailers, gyms, and distribution centers use these systems to manage heat loads while keeping energy bills in check.
Residential Installations
Evaporative coolers are ideal for Phoenix homes, especially those without ducted systems. They offer quiet, low-cost cooling that’s environmentally sound.
Data Centers and Electronics Rooms
Where humidity and heat need balance, hybrid systems can combine direct and indirect evaporative methods to maintain precise thermal envelopes.
Innovations in Evaporative Cooling Technology
Premier Industries, Inc. has been on the cutting edge of evaporative cooling innovation for over 30 years. Our systems feature:
- Stainless Steel Construction: Lifetime housing durability in even the harshest desert conditions.
- Advanced Cooling Media: Long-life rigid pads with antifungal coatings and high saturation efficiency.
- Custom Engineering: Tailored air-handling, ductwork, and control solutions to fit your building envelope and environmental demands.
We also assist with complete HVAC integration, ensuring that our evaporative coolers can work in tandem with other building systems and energy recovery technologies.
How to Design an Effective Direct Evaporative Cooling System
Proper system design is essential to achieve optimal performance and longevity.
Step 1: Load Calculation
Determine the heat load of your space (in BTU/hr or tons). Include internal gains from people, equipment, and solar exposure.
Step 2: Site Assessment
Evaluate ambient conditions, including:
- Dry-bulb and wet-bulb temperatures
- Humidity
- Air quality and particulate levels
- Noise restrictions
Step 3: Airflow Sizing
Size the system to deliver enough CFM to achieve the necessary air changes per hour (ACH) for cooling, ventilation, and humidity control.
Step 4: Media and Housing Selection
Select pad thickness and material based on desired saturation efficiency and air velocity. Stainless steel casings are optimal for harsh environments.
Step 5: Controls and Automation
Modern evaporative coolers can be equipped with:
- Variable-speed drives
- Smart thermostats
- Water quality sensors
- Remote monitoring
These features improve performance, reduce operating costs, and simplify maintenance.
Why Choose Premier Industries, Inc.?
Based in Phoenix, Arizona, Premier Industries, Inc. has specialized in the design and manufacture of direct evaporative cooling systems for over three decades. We are proud to offer:
- Lifetime Stainless Steel Housings for unmatched durability
- High-Efficiency Cooling Media with saturation levels up to 98%
- Custom Engineering & Design Services to suit any evaporative cooling or air-handling need
- Arizona-Based Manufacturing with fast turnaround and local expertise
- Comprehensive Support for installation, design, and maintenance
Our solutions have been deployed across commercial, industrial, and residential applications—offering reliable, cost-effective cooling in even the most demanding climates.
Ready to Upgrade Your Cooling System?
If you’re looking for a reliable, efficient, and cost-effective cooling system tailored to your needs, Premier Industries, Inc. is your partner of choice. Whether you’re outfitting a new facility, retrofitting an old one, or simply exploring alternatives to traditional air conditioning, our team is here to help.
Let us engineer a custom system that fits your airflow, temperature, humidity, and energy goals.
Call us today to speak with an expert and request a quote.
Stop wasting energy on inefficient HVAC systems—cool smarter with Premier Industries, Inc.
Categorised in: Evaporative Coolers, Evaporative Cooling
This post was written by Mike Nicolini
Comments are closed here.